Workshop
I invite you to my world.
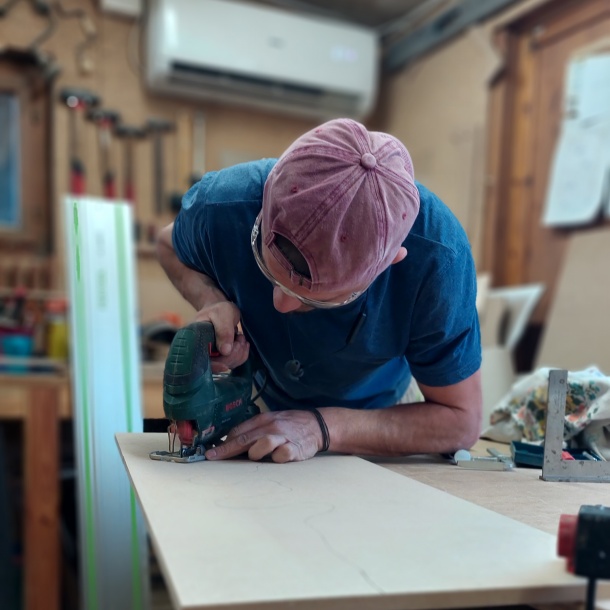
Welcome to my workshop
Let me take you to the place where my works are created. Take a moment and learn more about my work and the philosophy with which I create all these works.
"Something always seems impossible until it's done."
Nelson Mandela
Wood selection
Where does it start? And from the choice of wood. What kind of wood is this? The wood I choose is various hardwood species, sometimes with elements of the so-called burl. What is burl? Wood with burl is nothing more than material resulting from the swelling of the trunk. Growths, thickenings and bulges form on the tree, causing the arrangement of wood fibers and the pattern of the rings to change significantly. Therefore, characteristic patterns, spots, small knots and spiral patterns are formed under the bark. Such wood is healthy, but with a significantly changed structure. This turn of events makes burl wood highly valued.
Material purchase
The next step is to purchase the material and bring it to a condition in which you can start work. We're talking about humidity and drying. This is the next, very important step in the whole game. In order for our work to survive in the best possible condition in residential conditions, the wood from which my products are made must be dried to a humidity of 6 - 10%. Living conditions today are very different from those of twenty or thirty years ago. Super efficient underfloor heating and air conditioning systems cause a huge drop in air humidity in our homes, which has a direct impact on wooden objects there. The table below will help you understand what this is all about.
wood humidity
An example table of wood humidity in relation to the conditions in the apartment.
The best range for both wooden furniture and our well-being and health is marked in blue.
air temperature: relative air humidity: |
10oC | 15oC | 20oC | 25oC | 30oC |
20% | 4,7% | 4,7% | 4,6% | 4,4% | 4,3% |
30% | 6,3% | 6,2% | 6,1% | 6,0% | 5,9% |
40% | 7,9% | 7,8% | 7,7% | 7,6% | 7,5% |
50% | 9,4% | 9,3% | 9,2% | 9,0% | 9,0% |
60% | 11,1% | 11,0% | 10,8% | 10,65% | 10,5% |
70% | 13,3% | 13,2% | 13,0% | 12,8% | 12,6% |
80% | 16,2% | 16,3% | 16,0% | 15,8% | 15,6% |
90% | 21,2% | 20,8% | 20,6% | 20,3% | 20,1% |
You can read about the terms of use HERE
Creation conditions
Nowadays, it is impossible to use wood that has only been dried in the air. Depending on weather conditions, it may be around 15%, which is too high to be able to make furniture from it that will withstand living conditions. As the creator of this beautiful furniture, I recommend that we take care of the humidity level in our homes. It is best to keep it at 40 – 60%. The microclimate created in this way has a positive effect on people's well-being and health. Depending on the material, drying takes several weeks or longer. Afterwards, the material must relax and rest. My air-conditioned and heated workshop allows me to maintain good conditions for working with wood. Many people approach this topic with disregard, which may result in later problems in the form of bending, cracks and other damage to the furniture. That's why this is one of the most important stages of creation in Frogmakes, which I carry out with great care.
Project visualization
Now it's time for visualization. This is the moment when I see a piece of wood for the first time, close my eyes and try to imagine what the future piece of furniture or other product will look like. This is a very important moment for me in my entire journey of creation. This is the first emotional moment in my creation process. This is also part of the Frogmakes philosophy, to be able to create objects with soul.
I'm starting work
Now it's time to start working. Planning, shaping, carpentry, selecting legs, frames, design. My favorite moment is when I see the beauty of wood while processing the surface. It always surprises me. I make all cavities and fillings in such a way that their appearance is as natural as possible. He uses filling materials with the most natural composition possible. The imperfections left are not the result of carelessness, but of maintaining the most natural appearance possible. I try to preserve and highlight the most beautiful elements and details in wood. This is also the moment when I make the template according to which the glass will be made. It's a time-consuming and thorough process full of planning and vision.
Why glass?
Because it is natural, and in times when epoxy resin literally flooded the market of tables and other furniture, my glass design is rare today. A subtle and delicate combination of glass and beautiful wood makes my furniture unique. Glass is a natural product. It is nothing more than a combination of quartz sand, calcium and soda. At high temperatures, salt decomposes, producing sodium and calcium oxides, which then react with sand. The resulting mixture of sodium and calcium silicates creates glass. Various compounds are used to give color. The combination of gold and copper produces a red color, while the combination of iron and chromium produces green glass, while the combination of manganese and nickel colors the glass purple. Speaking of glass. This is the green tempered glass I chose, the so-called safety glass. Cut according to my template. Each shape is saved by me in my customer database and I can make the same glass at any time in case of damage, which means you don't have to worry in the future.
Surface protection
All work must now be secured and prepared for use. Depending on the product and surface, these are oils, hard oil-waxes, waxes made of natural ingredients approved for contact with food and completely safe. I chose products from renowned brands such as Rubio Monocoat, Borma Wachs, Odie's Oil, which provide the best results. I want to maintain the feel of the wood along with maximum protection. This is part of the Frogmakes philosophy.
Packing for shipping
It's time to pack. I send my works in wooden boxes, properly protected against damage during the long journey. Such shipment is, of course, more expensive than a regular box, but it better protects my product during transport. I can't imagine that after all the journey we've come, me and my work could now be destroyed before it reaches its new home. By the way. When I close the box and see my work live for the last time, there is some strange feeling, I don't know, hmmm...
End of work
APPROX. Now you know how I work and that I approach my work very professionally and emotionally, which allows me to create truly beautiful and unique projects in which I give a part of myself.
Okay, enough of this, time to get to work.
„I give wood a second life. You give him a place in Your home”
Krzysztof Grabowiec Frogmakes